Warehouse Management System (WMS) is designed to help reduce costs through effective warehouse processes. It is aimed at those companies that need to receive and ship goods, while maintaining an optimum utilization of space and knowing specifically where all goods are stored at any given time.
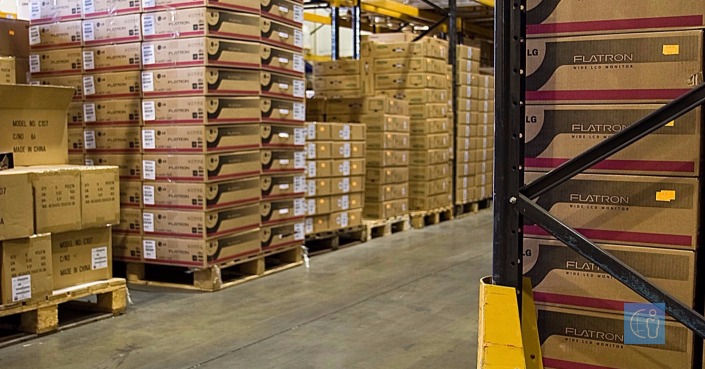
Basic objects
Bin
A bin is a storage device designed to hold discrete parts. It can be a space on a shelving unit that is portioned with physical dividers, or it can be any space defined within the warehouse to hold items. Each bin must have a type attached.
You can also determine whether the bin content in a bin is fixed or floating. A fixed bin is one that holds an item or items that have been dedicated to it.
It is predefined which specific item(s) can be placed in fixed bins, whereas floating bins are non-discriminatory – they have no particular items assigned to them.
Location
A physical structure or place where inventory is received stored and shipped.
Zone
Zone is a continuous area within a warehouse location that is usually distinguished from adjoining areas by the function for which it is used.
Documents Used in the Warehouse Management System
Source Documents
Items come to or leave a warehouse location on the basis of decisions made elsewhere in the company. The details of these decisions are recorded in source documents, which are released to the warehouse before items can be received or shipped. The source documents for receipts are purchase orders, sales return orders or inbound transfers. The source documents for shipments are sales orders, purchase return orders or outbound transfers.
You can track the progress of source documents released to the warehouse. In the source document, click Order and then Whse. Receipt Lines or Whse. Shipment Lines, depending on whether a receipt or a shipment is the expected outcome of the source document. You can then view any shipment lines or receipt lines that have been created in the warehouse, if any. If there are no lines, the items have not yet arrived in the case of receipts, or the warehouse has not yet begun to prepare the shipment.
Warehouse Receipt
In the Warehouse Receipt window, you record the receipt of items into the warehouse.
You retrieve source document lines into this window, enter the quantity being received in the Qty. to Receive field, and then post the receipt of the items.
During posting, the program updates the quantity fields on the source documents, records the items as part of company inventory, and sends the receipt lines to the warehouse put-away function.
Shipments
Here, you prepare shipments requested by source documents when your warehouse is set up to require shipment processing with warehouse documents. If your location requires pick processing, you can create pick instructions shipment by shipment, or you can release shipment lines to the pick worksheet where you can plan a more efficient pick round for a number of shipments. When employees have picked all the items, you can finish preparing the shipment and then post it.
Put-aways and Picks
These two menu items contain the instructions that warehouse employees must follow when moving items around the warehouse. The warehouse put-aways are used when the location is set up to require both warehouse receipt and warehouse put-away processing, and warehouse picks are used when the location is set up to require both warehouse picking and warehouse shipment processing.
When your location is set up to use bins, the instructions suggest the bin from which you should take an item and the bin in which to put it. If you are using directed put-away and pick, this suggestion is based on calculations the programs makes using bin ranking or put-away templates, depending on the activity. If you are not using directed put-away and pick, the suggestion is based on the item's default bins. You can always modify the instructions the program has suggested.
If your warehouse is set up for directed put-away and pick, you can use an automatic data capture system to facilitate putting away and picking items within the warehouse.
Warehouse processes
Warehouse Receipt Process
The inbound flow of the warehouse begins with the items coming into the warehouse and the warehouse personnel registering those items into the program. Each item is identified and matched to a corresponding inbound source document. An inbound source document can be one of the following three types: purchase order, inbound transfer, or sales return order.
The process is described in the following steps:
Warehouse Inbound Request. During the release of the purchase order (sales return order, inbound transfer order), an inbound warehouse request is created by the program. It contains references to the source document type and number and is not visible to the user.
Warehouse Receipt. Goods arrive in the warehouse and in the warehouse receipt order window the responsible employee makes a request to the program to retrieve the necessary source document lines. Based on this inbound warehouse request, warehouse receipt order lines are created and displayed in the warehouse receipt order window.
The employee can update the created warehouse receipt order, fill in “qty. to handle” (this can be done automatically if allowed by the warehouse setup per location), and select the receiving zone and bin.
Receipt Posting. From the Warehouse Receipt window, the employee can use the “Post” function: The purchase order (inbound transfer order, sales return order) is posted as received, and a posted receipt and a posted warehouse receipt order are created. The warehouse receipt order cannot be deleted until the quantity registered in the warehouse is posted as received and put away. A warehouse receipt order line is deleted if it is completely posted and put away. If all warehouse receipt order lines are completely posted as received and put away, the warehouse receipt order is deleted.
The employee selects the lines to put away and then fills in the "qty. to handle". (Note: The program will automatically fill this in if it is set up per location.)
Warehouse Shipment Process
The outbound flow in the warehouse begins with a request for shipment in the form of a sales order, an outbound transfer order or a purchase return order. The warehouse personnel will go directly to the Warehouse Shipment window to retrieve lines from these source documents. The process is described in the following steps:
Warehouse Outbound Request. During the release of the sales order (purchase return order, outbound transfer order) an outbound warehouse request is created. It contains references to source document type and number and is not visible to the user.
Warehouse Shipments. In the Warehouse Shipment window, the warehouse manager instructs the program to retrieve source document lines that need to be shipped. The manager has the possibility to combine several source document lines into one warehouse shipment order.
The warehouse manager decides to start the picking process for some shipment orders, selects the lines to be picked and specifies a bin to place picked items (a shipping bin or an staging bin).
The warehouse manager enters the qty. to handle on the pick assignment lines (which can be filled in automatically if this is permitted by the location’s warehouse setup), specifies a picking method for optimization of the warehouse handling, and then goes to the Create Pick function. Warehouse instructions are created and pick lines are deleted (if fully assigned).
Pick. The warehouse employee picks items according to the warehouse instructions and posts the documents. If picking was initiated by a warehouse shipment order, the status of the corresponding warehouse shipment header is changed to “Completely Picked”, “Partially Picked”, “Partially Shipped”, or “Completely Shipped.”
Ship. After the items have been picked and moved to shipping bins, the user goes to the post shipment function. Sales orders, transfer orders and purchase return orders are posted as shipped. A posted warehouse shipment is created, and the warehouse shipment is deleted when it is fully posted. The outbound warehouse request is deleted if fully handled, and warehouse entries are created.
For glossary of WMS terms, click here ...